With Fall season coming to a close and poinsettias going out the door, many growers are already gearing up for young plant production and early spring sales. Regardless of when your doors reopen and plants start filling greenhouse space, it is imperative to establish and maintain a clean growing environment. GGSPro works with ornamental growers of all sizes and production styles across the country. In all cases, the first step to every successful integrated pest management strategy is to prevent any carryover pests from the previous season or crop cycle. Thus, a comprehensive sanitation procedure is needed to ensure a new crop cycle starts clean. In this article we will provide sanitation tips and strategies that can help to bolster your interseason sanitation approach or cover areas commonly overlooked that may harbor pests between seasons.
Physical Cleaning
There are three prongs to a successful sanitation program: physical cleaning of the production area, chemical cleaning, and disinfecting. The first and most arduous work is the physical cleaning of the production area. In this step, we work through the debris and chaos from the prior season or crop cycle. It should be a “clean sweep” where growers power wash and remove all debris and leftover material (e.g., containers, tags, media, fallen plant material, etc.) from the production area. It’s worth noting that this part is essential for the remaining sanitation steps to be successful. In almost every case, cleaners should be applied so that contact time is prolonged (i.e., cool and cloudy days). Cleaners, which are generally a combination of strong acids or bases with detergents, should be washed off with clear water before drying or they can leave a considerable residue on hard surfaces. Surfactant or oxidizer-based sanitizers can commonly be left to dry once applied, but it is important to follow all label instructions to ensure equipment, employee, and plant safety.
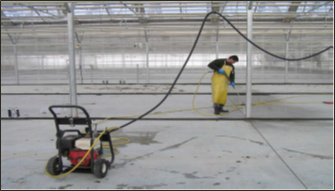
Figure 1: Hard surface sanitation with pressure washing equipment
Foaming is Fun
Foaming continues to gain momentum in sanitation practices for several reasons: it allows the applicator to see exactly where are they sprayed/applying (preventing accidental or reapplications), it allows chemicals to fight gravity and stick to vertical surfaces more easily, and it also tends to be more enjoyable than conventional spraying. Foaming can be achieved by using various pieces of technology – many of our professional cleaners already have detergents in them, making them easy to foam as well. Dramm’s FM20 Foamer is great for foaming large area quickly with the help of an air compressor. For spot foaming small areas, Dramm’s Compression Foamer is very similar to using a hand pressurized pump sprayer. If directly injecting from the bottle or injecting from a stock tank, a HydroFoamer is a simplistic cost-effective device where a spray nozzle can be connected to a hose end to automatically produce a foam consistency (Figure 2). BioSafe’s BioFoamer agent can be used in tandem with various foaming equipment to help enhance foam thickness. Foamers can be used to apply both cleaning products and sanitizers.
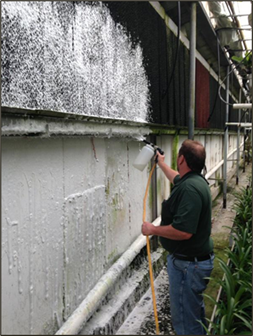
Figure 2. Foaming an evaporative cooling pad using a Hydrofoamer
Keys Areas to Consider Foaming
Contact and coverage are key with both cleaners and sanitizers. Thoroughly apply these to benches, concrete floors, cooling pads, ground cover fabrics, and other non-porous surfaces in the production area. For cleaners, allow a minimum of 3 to 5-minute treatment time and follow up with a clean water wash down. If you are using a fan and pad evaporative cooling system, you know how fowled evaporative cooling pads get unless proper maintenance is implemented. Remember, wherever there is water, biofilm and algae can follow. Couple this with mineral scale, which is very common for high alkalinity irrigation sources, and we can quickly reduce the efficacy of our equipment (Figure 3). Similar to other surfaces and irrigation lines, we need to rely on a strong acid-based cleaner to help physically remove or dissolve this combination of contaminants that has developed. Foaming is a great way to ensure the cleaner or sanitizer being applied has longer contact time on vertical surfaces. Underneath benches where there is excessive buildup of algae, soil media or gravel is also another area that growers forget to sanitize, but they are a haven for carrying over issues. Clean and rinse out irrigation lines first before going back in with foaming floor surfaces. Rinse the cleaning solution down once a thick layer of foam has had adequate contact time to clean these production spaces.
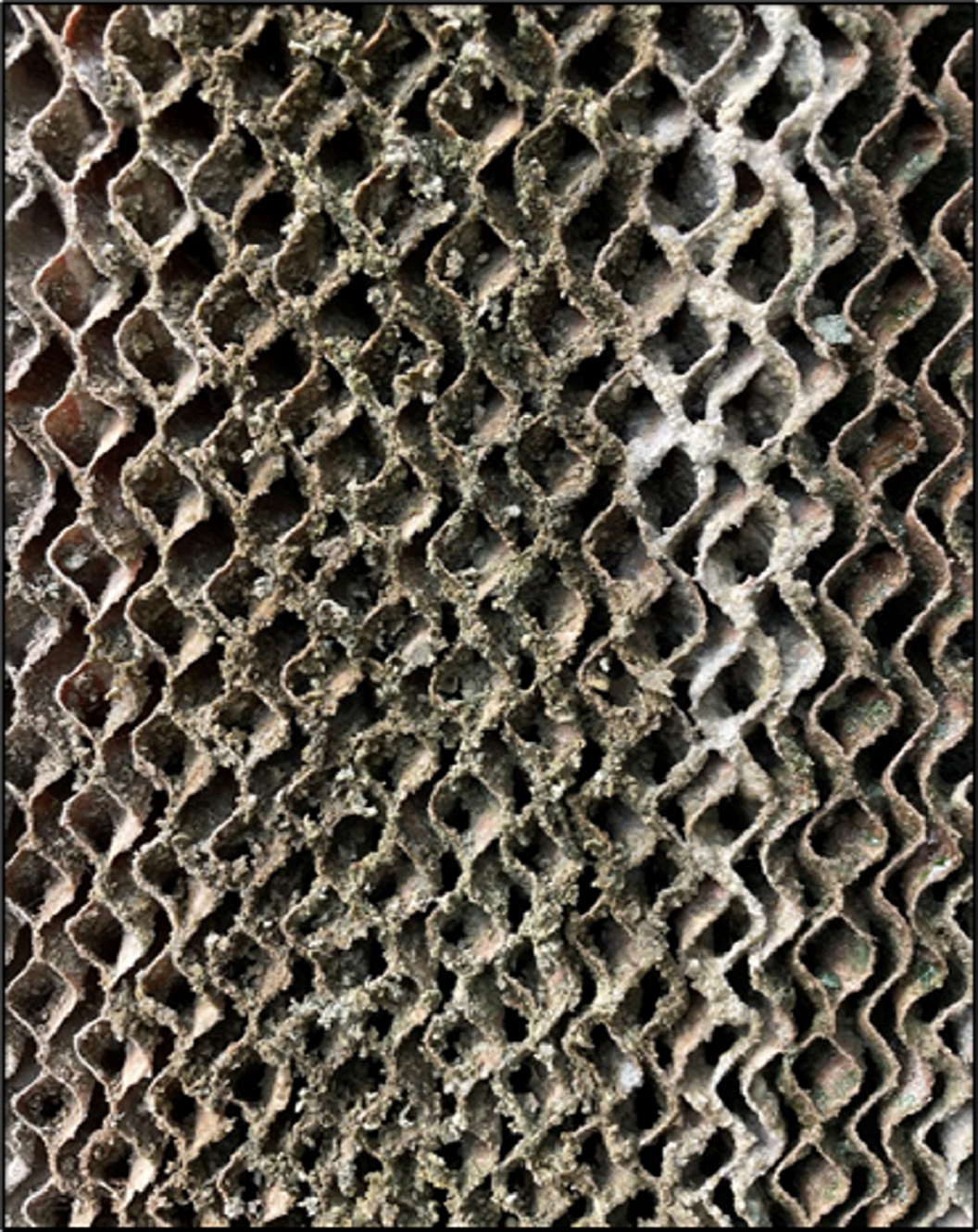
Figure 3. Clean (left) and fowled (right) evaporative cooling pad.
Herbicide Applications & Disinfecting After Cleaning
Once the greenhouse has been physically and chemically cleaned, applying an appropriately labeled herbicide for post and pre-emergent (e.g., Marengo or SureGuard EZ) weed control is recommended. Contact GGSPro for a full list of herbicides labeled for greenhouse use – the appropriate product can depend on your needs and situation. The final step of applying a sanitizing agent to hard surfaces such as benches, sidewalls, and irrigation lines will ensure thorough disinfection. ZeroTol 2.0, SaniDate 5.0, SaniDate 12.0, or KleenGrow can be used as effective choices. These products are applied and left to air-dry on the treated surfaces leaving behind no chemical residues. Please reach out to your local Griffin sales representative or GGSPro for specific usage rates.
* Additional sizes are available
Note: Avoid crop contact with chemical cleaners, as these products will cause crop damage & are not approved for crop application. Always ensure that staff utilize proper PPE, the required PPE for the products can be found within the label. Not all products are registered in all states. Some pesticides are restricted use in some states or regions and not others. It is the responsibility of the applicator to read and follow all label directions, remembering that labels may change. Other products may be safe and effective. Rates, application methods, and edible status are detailed in our GGSPro Insecticide & Fungicide Guides. Griffin also offers the 5th Edition GGSPro Technical Reference Guide in both English and now Spanish versions. This valuable resource outlines a wide range of pest control options and information on pollinator safety, BCA’s, scouting, weed management, plant lighting, nutrition, water quality and more!
Physical Cleaning
There are three prongs to a successful sanitation program: physical cleaning of the production area, chemical cleaning, and disinfecting. The first and most arduous work is the physical cleaning of the production area. In this step, we work through the debris and chaos from the prior season or crop cycle. It should be a “clean sweep” where growers power wash and remove all debris and leftover material (e.g., containers, tags, media, fallen plant material, etc.) from the production area. It’s worth noting that this part is essential for the remaining sanitation steps to be successful. In almost every case, cleaners should be applied so that contact time is prolonged (i.e., cool and cloudy days). Cleaners, which are generally a combination of strong acids or bases with detergents, should be washed off with clear water before drying or they can leave a considerable residue on hard surfaces. Surfactant or oxidizer-based sanitizers can commonly be left to dry once applied, but it is important to follow all label instructions to ensure equipment, employee, and plant safety.
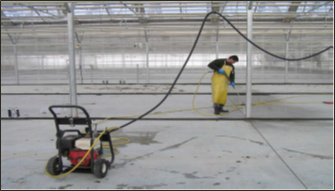
Figure 1: Hard surface sanitation with pressure washing equipment
Foaming is Fun
Foaming continues to gain momentum in sanitation practices for several reasons: it allows the applicator to see exactly where are they sprayed/applying (preventing accidental or reapplications), it allows chemicals to fight gravity and stick to vertical surfaces more easily, and it also tends to be more enjoyable than conventional spraying. Foaming can be achieved by using various pieces of technology – many of our professional cleaners already have detergents in them, making them easy to foam as well. Dramm’s FM20 Foamer is great for foaming large area quickly with the help of an air compressor. For spot foaming small areas, Dramm’s Compression Foamer is very similar to using a hand pressurized pump sprayer. If directly injecting from the bottle or injecting from a stock tank, a HydroFoamer is a simplistic cost-effective device where a spray nozzle can be connected to a hose end to automatically produce a foam consistency (Figure 2). BioSafe’s BioFoamer agent can be used in tandem with various foaming equipment to help enhance foam thickness. Foamers can be used to apply both cleaning products and sanitizers.
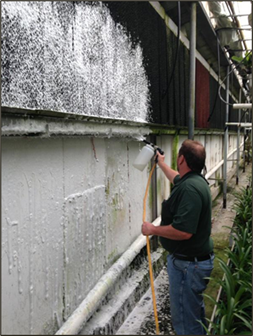
Figure 2. Foaming an evaporative cooling pad using a Hydrofoamer
Keys Areas to Consider Foaming
Contact and coverage are key with both cleaners and sanitizers. Thoroughly apply these to benches, concrete floors, cooling pads, ground cover fabrics, and other non-porous surfaces in the production area. For cleaners, allow a minimum of 3 to 5-minute treatment time and follow up with a clean water wash down. If you are using a fan and pad evaporative cooling system, you know how fowled evaporative cooling pads get unless proper maintenance is implemented. Remember, wherever there is water, biofilm and algae can follow. Couple this with mineral scale, which is very common for high alkalinity irrigation sources, and we can quickly reduce the efficacy of our equipment (Figure 3). Similar to other surfaces and irrigation lines, we need to rely on a strong acid-based cleaner to help physically remove or dissolve this combination of contaminants that has developed. Foaming is a great way to ensure the cleaner or sanitizer being applied has longer contact time on vertical surfaces. Underneath benches where there is excessive buildup of algae, soil media or gravel is also another area that growers forget to sanitize, but they are a haven for carrying over issues. Clean and rinse out irrigation lines first before going back in with foaming floor surfaces. Rinse the cleaning solution down once a thick layer of foam has had adequate contact time to clean these production spaces.
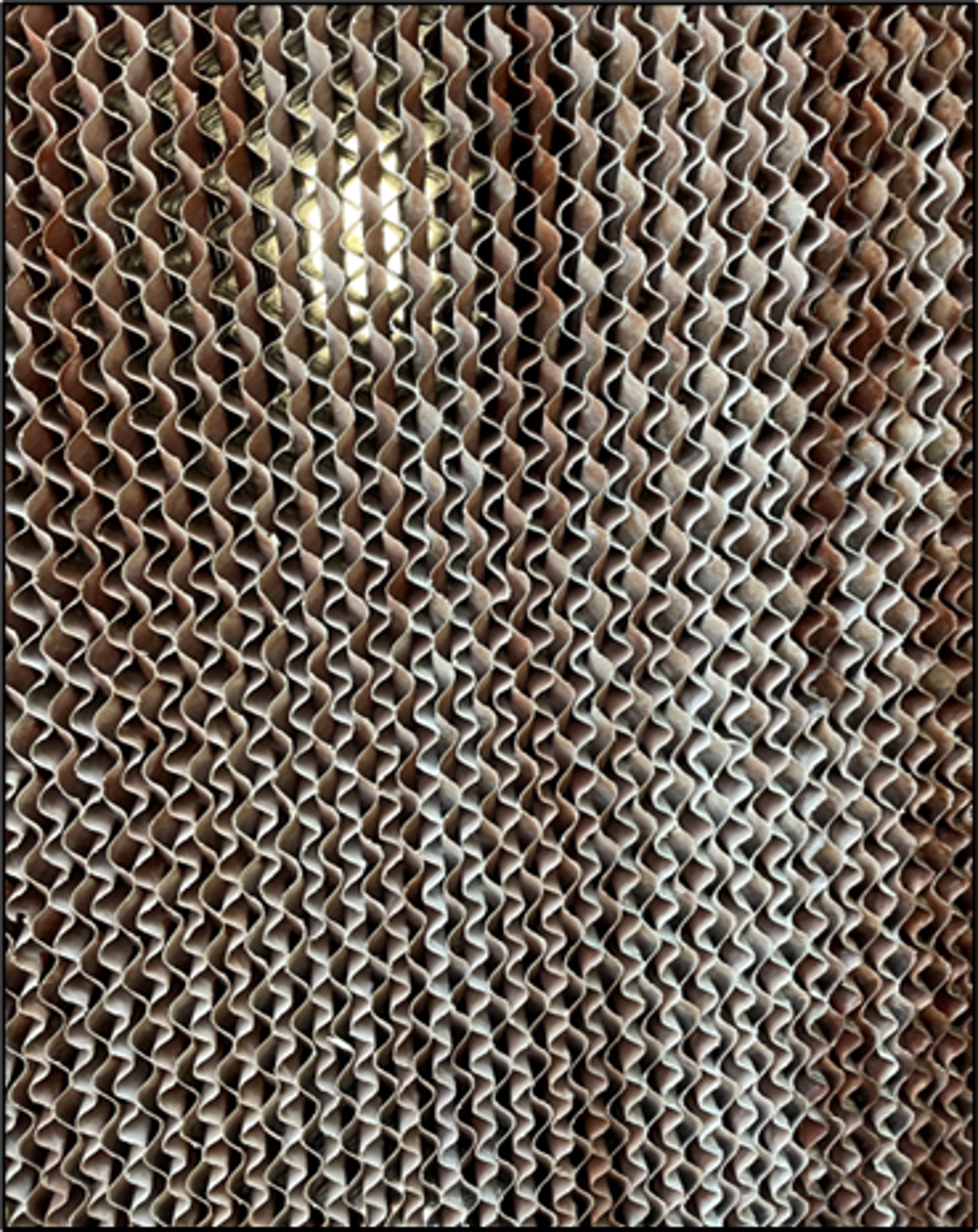
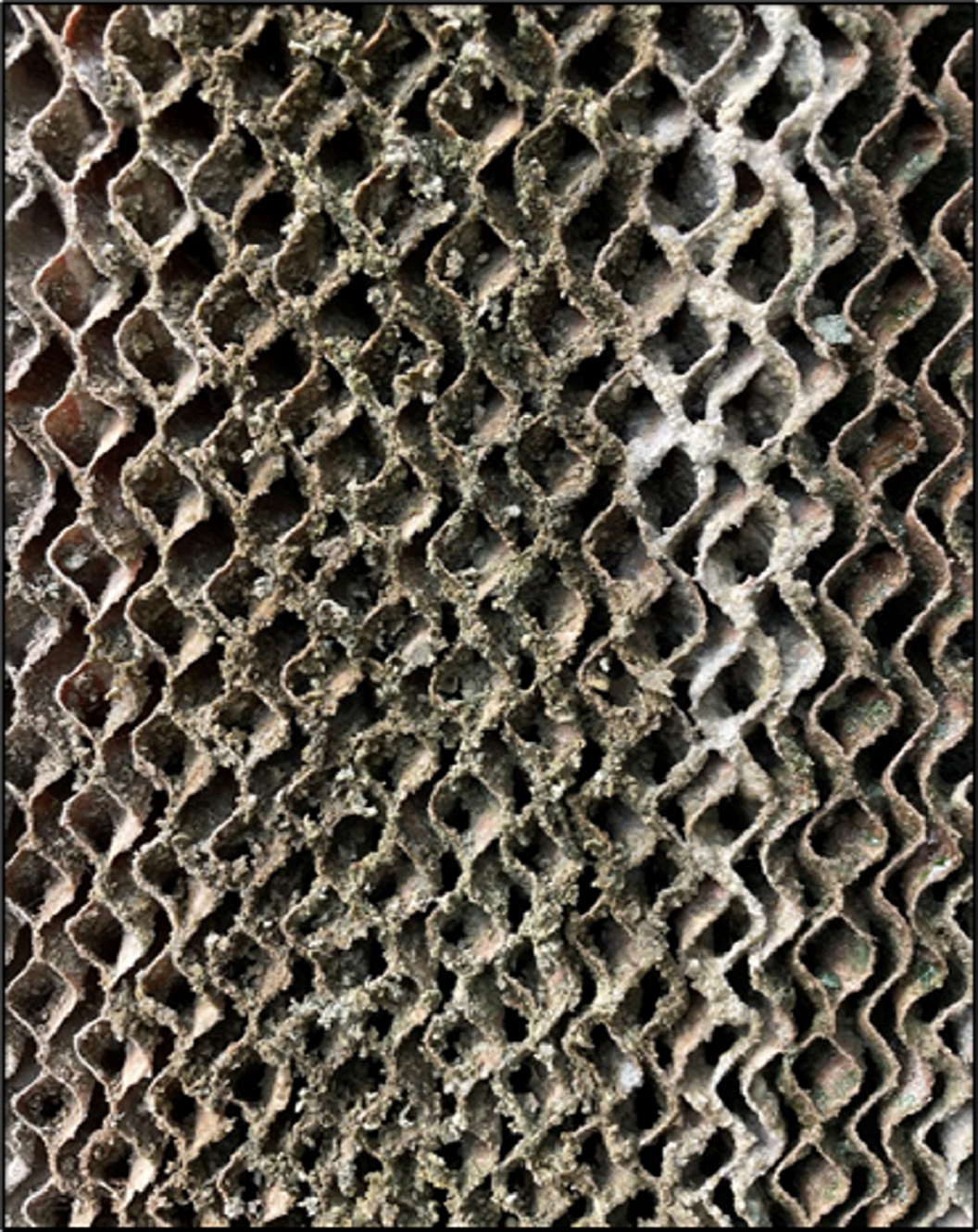
Figure 3. Clean (left) and fowled (right) evaporative cooling pad.
Herbicide Applications & Disinfecting After Cleaning
Once the greenhouse has been physically and chemically cleaned, applying an appropriately labeled herbicide for post and pre-emergent (e.g., Marengo or SureGuard EZ) weed control is recommended. Contact GGSPro for a full list of herbicides labeled for greenhouse use – the appropriate product can depend on your needs and situation. The final step of applying a sanitizing agent to hard surfaces such as benches, sidewalls, and irrigation lines will ensure thorough disinfection. ZeroTol 2.0, SaniDate 5.0, SaniDate 12.0, or KleenGrow can be used as effective choices. These products are applied and left to air-dry on the treated surfaces leaving behind no chemical residues. Please reach out to your local Griffin sales representative or GGSPro for specific usage rates.
Item Name | Item Number | Comments |
---|---|---|
Strip-It PRO | 74-2125* | Cleaners: No plant contact. Targets debris, biofilm, and algae on hard surfaces and plastics. |
AgH PRO | 74-2105 | |
GreenClean Acid Cleaner | 74-2040 | |
GreenClean Alkaline Cleaner | 74-2045 | |
GreenClean Pro | 74-20521 | No plant contact. Targets debris, biofilm, and algae on hard surfaces. Does not need to be rinsed once broadcasted – apply to wet surfaces. |
ZeroTol 2.0 | 71-35501* | Sanitizers: All surfaces including areas of crop contact. Targets algae, bacteria, and fungi on hard surfaces, plastics, and tools. |
KleenGrow | 74-21101* | |
SaniDate 5.0 | 71-35001* | |
SaniDate 12.0 | 71-35351 | |
Marengo | 72-2809* | Herbicides: Read specific label instructions when applying in enclosed spaces. |
Marengo G | 72-28181 | |
SureGuard EZ | 72-8212* | |
BioFoamer | 74-1360 | |
HydroFoamer | 74-2103 | |
Dramm Compression Foamer 8L | 74-2688 | |
Dramm FM20 Foamer | 74-2689 |
Note: Avoid crop contact with chemical cleaners, as these products will cause crop damage & are not approved for crop application. Always ensure that staff utilize proper PPE, the required PPE for the products can be found within the label. Not all products are registered in all states. Some pesticides are restricted use in some states or regions and not others. It is the responsibility of the applicator to read and follow all label directions, remembering that labels may change. Other products may be safe and effective. Rates, application methods, and edible status are detailed in our GGSPro Insecticide & Fungicide Guides. Griffin also offers the 5th Edition GGSPro Technical Reference Guide in both English and now Spanish versions. This valuable resource outlines a wide range of pest control options and information on pollinator safety, BCA’s, scouting, weed management, plant lighting, nutrition, water quality and more!